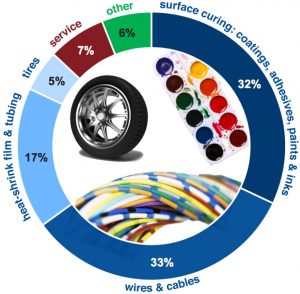
Current end-use market distribution of electron beam industrial applications. 87% of e-beam process involves crosslinking, represented by the applications in blue segments. Image source: IAEA Working Material on Industrial Electron Beam Processing
Electron beams are an exceptional source of energy that are capable of initiating chemical reactions without the need for catalysts, high temperature or high pressure. The high kinetic energy and penetrating nature of the electrons provide significant benefits over typical chemical methods.
Electron beam processing involves the absorption of large doses of energy from accelerated electrons in materials in order to modify them in some beneficial manner. The main processes initiated by electron beam are polymer modification by crosslinking or scission, curing of coatings, decomposition of industrial effluents or synthesis of a new substance. Some materials that have been successfully processed via electron beam include plastics and rubber, wire and cable insulation, crosslinking of ultra-high molecular weight polyethylene for hip and joint replacement in the medical industry and many more. Beneficial changes produced in treated materials are improved thermal and chemical resistance, stability at elevated temperatures, improved tensile strength and other mechanical properties. Electron beam technology provides an efficient, safe and environmentally friendly way to drive chemical reactions.
E-beam accelerator sales eclipse $2 billion annually and provide added value to products of more than $500 billion every year (RW Hamm, Industrial Accelerators and Their Applications, 2012). However, adoption of e-beam technology has been relatively slow because of a general lack of knowledge of the technology. Also, old conventional e-beam accelerators that are still available on the market have limitations in that they are not energy efficient, take up a large foot print and can be complicated to use and maintain.
Accelerator technology has applications in water and biosolids treatment, cargo scanning, material modification using electron beams, medical sterilization (X-ray and electron beam), industrial electron-beam driven chemistry, advanced manufacturing, environmental remediation and food sterilization.